Keywords:Hardness,qualified,low hardness,high hardness,tempering,cooling,tempere,heat treatment,heating,temperature,heat preservation,mixing
Causes of unqualified hardness and preventive measures against unqualified hardness
In the practice of heat treatment production, it will produce various defects, such as cracking, severe deformation, unqualified hardness and unqualified performance, etc. Different defects have the same causes, and the corresponding preventive measures are also different. This article briefly analyzes the causes and prevention methods from the most common defects-unqualified hardness.
There are two cases of unacceptable hardness: too high hardness and too low hardness.
1. The hardness is too high:
1. Mixing: For example, carbon steel is mixed with alloy steel, and the hardness should exceed our expected value. It can be tempered again according to the actually detected hardness and tempering parameters.
2. Material modification: Alloy steel is used to replace carbon steel, but the information of material replacement is not correctly transferred to the heat treatment process.
After contacting the relevant departments and implementing the actual materials, re-temper.
The above two situations are indeed management problems, and the heat treatment process cannot be solved.
3. Insufficient tempering temperature or time:
⑴ The equipment has hidden problems, and the actual furnace temperature is low. Recalibrate the temperature control system.
⑵ The tempering time is insufficient or the tempering temperature is low, which results in partial hardness of the workpiece. The reason is that the tempering process parameters are not accurate when the furnace is produced in production, and the tempering time of some or all of the workpieces is short, resulting in high hardness. At this time, it is necessary to accurately calculate the tempering time and temperature of each workpiece, select an appropriate temperature and holding time for tempering, and ensure that the hardness of each workpiece meets the requirements.
Second, the hardness is too low:
This is the most likely quality problem in production, and it is not easy to find the cause of the problem. It is more harmful to production (wasting energy and affecting production progress), and it is also the most headache.
1. Material problems, their causes and preventive measures are the same as above. If the hardness of the test does not exceed 140HB, such materials can be thrown away directly, and even spark discrimination is not required.
2. Quenching problem of heat treatment process:
The workpiece must ensure that the hardness meets the requirements after tempering. The prerequisite is that the quenching must meet the specified requirements, and it must be at least 50HB higher than the final hardness limit before it can pass the tempering. This is the most prone to problems in our production, and the most easily overlooked. People often answer me: "It's been quenched like this all the time, I don't know why it is not qualified today?" The problems that are easy to occur in the quenching process are as follows:
⑴The heating temperature is insufficient.
More common is a fluke mentality, thinking that the temperature is about the same, maybe it can be quenched. It is believed that the color of the workpiece is also low during normal quenching, and it is also quenched. As everyone knows, forgetting that pre-cooling of austenite is not the same as incomplete austenitization and quenching. When the heating is insufficient, there is undissolved ferrite in the austenite, which is to reduce the quenching hardness; and the temperature during pre-cooling during the quenching is less than 800 ℃, but the supercooled austenite is not Ferrite will precipitate out. This is caused by insufficient understanding of austenite.
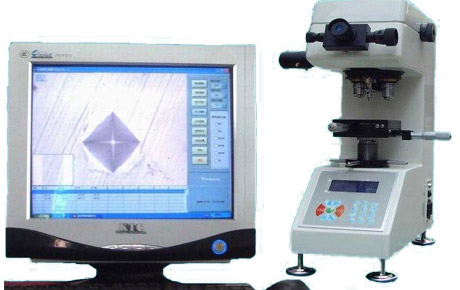
Unqualified hardness
⑵ Problems in cooling.
There is only one problem with cooling, and the cooling rate is insufficient. But there are many reasons for insufficient cooling speed:
Excessive pre-cooling: In order to prevent the workpiece from being quenched and cracked, it is very necessary to pre-cool before quenching. If the master is not good and it is lower than Ar1, the pre-eutectoid transformation occurs and pro-eutectoid ferrite occurs, which will reduce the hardness of the workpiece. At the same time, pre-eutectoid transformation is not allowed for the demanding artifacts. At this time, the tempering hardness according to the normal process will be lower than the specified value.
When pre-cooling, pay attention to observe the temperature of the workpiece, and also improve the ability to distinguish the temperature to avoid pre-cooling the workpiece below Ar1.
Insufficient cooling capacity in the cooling medium: Take quenching water as an example. First, when the water temperature is high (such as exceeding 30 ℃, which is the most easily overlooked situation in production), the cooling rate of the pearlite transformation area will be seriously reduced At that time, how to cool the workpiece, it is already inconsistent to want to harden (because part of the non-martensitic transformation has occurred). The second is that the densely packed workpieces, such as insufficient mobility in the medium, and the inability of steam to break the film, will result in insufficient hardening hardness of the parts, especially in the middle. It is necessary to pay attention to the temperature of the cooling medium at any time, observe the installation of the furnace, and take preventive measures in a targeted manner.
The above two situations will cause the cooling rate of the workpiece to cross the C curve in different ways. After quenching, a variety of mixed structures will be obtained, such as: ferrite + martensite, ferrite + pearlite + martensite, torrite + martensite, etc. The test hardness will be lower than the normal value.
⑶Quenching cooling time is shorter.
Due to the short cooling time, the temperature after the actual quenching of the workpiece is higher, but the quenching of the workpiece itself has not been completed, and the hardness after tempering is lower than normal. At the end of quenching, the temperature of the workpiece is generally lower than the Ms of the material, otherwise the hardness will be lower than normal after tempering. At the end of quenching, let the workpiece continue to air-cool for a while and observe the temperature of the workpiece. If the temperature is higher, additional cooling should be made to reduce the temperature of the workpiece to an appropriate level. Of course, those who have experience can distinguish the temperature of the workpiece from the time when the workpiece is discharged.
⑷ Problems in tempering.
The problems that occur in tempering are mainly reflected in the fact that the tempering time is too long or the temperature is high, and there are also equipment problems, such as: thermocouple withdrawal, large temperature control system control errors, etc.
The above only analyzes the reasons for the hardness of the workpiece after heat treatment is unqualified, there may be some reasons in actual production, we need to further improve our understanding, to analyze the causes and propose specific countermeasures. In short, after the hardness is unqualified, you should seriously analyze your production process, find out the reasons for improvement, and generally do not go to other people ’s reasons (and also offend people). Pay attention to the details, especially the usual practice. Only when the details are in place, will there be no or fewer quality problems. So say "details determine success or failure".
More Causes of unqualified hardness and preventive measures against unqualified hardness:http://www.industrial-furnace.com/articles/hardness_qualified.html
More Posts
2019-07-03 14:00:18
Common defects in quenching include oxidation, decarburization, defor...